PREPARATION OF PLANS FOR TECHNICAL PROTECTION SYSTEMS
Creating a technical protection plan involves strategic planning for implementing a technical protection concept, with a focus on selecting the optimal level of protection for a specific facility. The technical protection plan includes the following key aspects:
- Integration with other technical systems on the facility: The plan considers how the technical protection system connects and synchronizes with other technological components present on the facility. This aspect ensures coordination between different systems for comprehensive security.
- Alignment of technical protection systems with security: The plan rovides a detailed description of how technical protection systems communicate and cooperate with physical security, highlighting ways they mutualy adjust. This ensures efficient and synchronized operation.
- Requirements for non-system components affecting facility safety: In addition to the technical protection system, the plan identifies requirements that other components must meet in order to contribute to the facility’s safe functioning. This includes elements that are not directly part of technical protection, but have a significant impact on overall security.
- Construction and related criteria: The plan also includes specific requirements for construction and spatial conditions essential for implementing the technical protection system. This ensures that the infrastructure supports the smooth functioning of all protection systems.
Creating a technical protection plan requires a deep understanding of the facility’s characteristics, potential threats, and technological solutions. Precisely defining these aspects enables the effective implementation of the technical protection system and enhances the overall facility security.
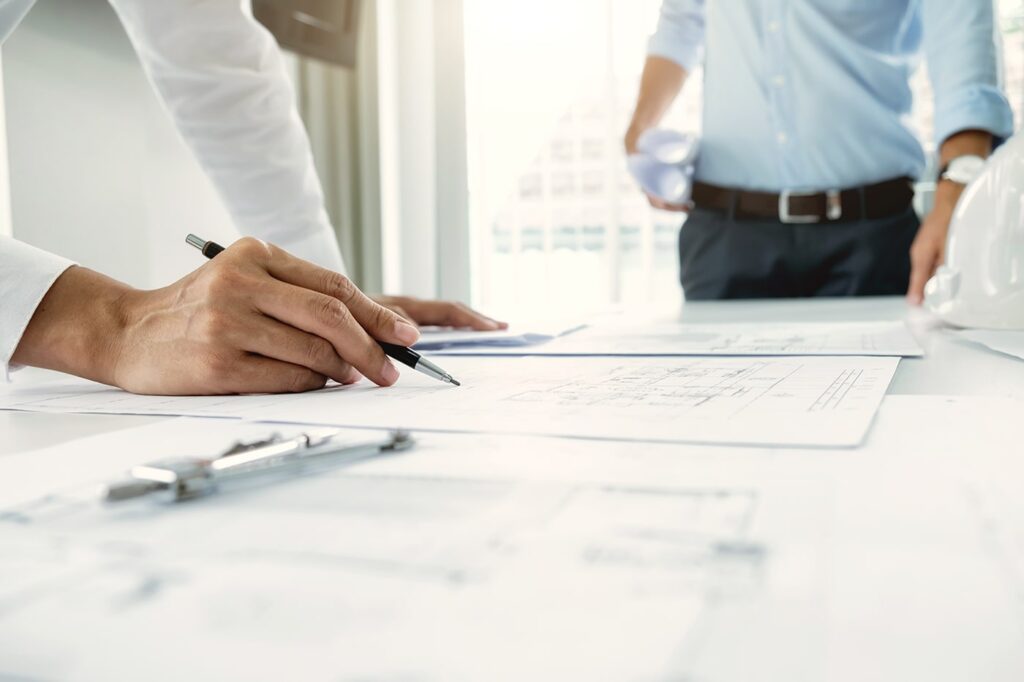
OF THE ACT ON RISK ASSESSMENT
The act on risk assessment is a pivotal element in the European approach to enhancing occupational safety and health protection for employees. It serves as the foundation for recognizing potential hazards in the workplace and implementing appropriate measures to prevent accidents and safeguard the well-being of employees.
Every employer, regardless of industry, the scope of business or the number of employees, is obligated to prepare a Risk Assessment Act for each workplace within the organization. This document plays a central role in the identifying, analyzing and managing workplace risks.
The process of creating the Act on risk assessment involves:
- Hazard identification: Thoroughly identifying all potential hazards and risks that employees may encounter while performing their tasks. These hazards can encompass physical, chemical, biological, ergonomic and psychosocial factors.
- Risk assessment: Evaluating the likelihood and severity of the consequences associated with each identified hazard. This allows for the prioritization of risk reduction measures.
- Defining control measures: Based on the risk assessment, identifying effective control measures that should be implemented in order to mitigaterisks to an acceptable level. These measures may include technical modifications, employee training, procedural changes, and more.
- Implementation of measures: Putting the defined control measures into practice at the workplace in order to reduce the identified risks. This may involve changes in work organization, equipment procurement, employee education, etc.
- Regular review: The risk assessment document should undergo regular reviews to ensure it remains current and respondive to changes in the environment, technology or business.
It is essential to emphasize that the Risk Assessment Act must be in compliance with applicable laws and regulations, while also being tailored to the specific needs of each organization. This document plays a critical role in creating a safe and healthy work environment, contributing to the protection of employees and reducing the risk of workplace injuries and accidents.